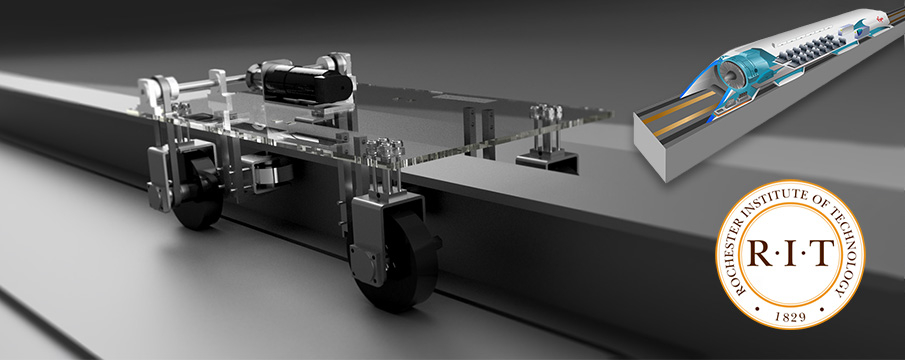
- Home
- Discover
- Your applications
- Case studies
- Case study: Hyperloop with USB3 cameras at 1225km/h
Hyperloop and the transportation of the future
Elon Musk created PayPal, worked with Tesla to make electric cars suitable for the mass market, and wants to fly to Mars in 2024. Yet the innovative investor and multi-billionaire still has big plans here on earth. His Hyperloop project aims to develop a high-speed transport system that will connect the cities of Los Angeles and San Fran-cisco in less than 30 minutes. It will be faster than flying and cheaper than the train. To bring this concept closer to reality team of engineers needed to monitor the structural integrity of the tubes in the near vacuum conditions. These tubes are used to transport the electrically powered passenger cabins so it is crucial to notice any changes that could impact safety. This task was tackled by the USB3 high-speed cameras.
Into the loop
A team from Musk's space exploration company SpaceX devised the fundamental concept of Hyperloop - a multi-passenger pod or capsules speeding through a series of depressurized tubes.Subsequent development involved participative approach with an open invitation to join, comparable to open source development method common in the software sector.
Applicants were encouraged to use existing technology to speed up the development cycle and keep down the costs.
Amongst various required technologies, SpaceX has expressed a need for a rail and sub-track visual observation system by which an operator could identify abnormalities or foreign object debris (FOD) on the track.
The RIT Imaging Hyperloop Team from the Imaging Science Center at the Rochester Institute of Technology is a USA-based research group specializing in imaging.
The 25-strong team submitted a bid as part of the Hyperloop process to implement the safety and maintenance system for the tunnel tubes.
With an automated camera system providing intelligent image analysis, at the beginning of 2016 the RIT team won the initial selection procedure and is now part of the Hyperloop testing program.
Team lead Kristina Carrucci said: "Our innovative approach was unique among the bidders. Thanks to fully automatic, totally imaging-based inspection we were able to win out against the competition. Other conventional methods, such as those normally used for inspection of oil pipelines, were not suitable for Hyperloop. We use structured light for 3D scanning of the pipe walls at high speed. This is normally used for reverse engineering or target/actual comparisons in industrial production and is commonly used to make 3D maps of stationary objects for scientific purposes, but has never been utilized at ultrasonic speeds."
Hyperloop test track under construction – Picture: Reuters
They feel the need ..
The team designs include a high-speed communications system and a sensor system detecting faults in the tube walls that could impede the motion of the pod.
Both are relatively new technologies applied in a higher speed environment.
The aim is to ensure rapid and precise monitoring of the surface condition of the inside of the tubes.
Any bulges, cracks, deformed weld seams or oxidation represent potential safety risks.
The structured light scanner is mounted on a robotic transportation system that shuttles the imaging solution down the rail.
The scanner is made up of a projector, which projects a grid of lines onto the tunnel walls, and 2 industrial high-speed cameras.
Based on the deformation of the projected pattern on the rail, the system can inspect the rails (without contact) for geometrical variations such as enlarged gaps between the tube sections (so called I-beam integrity scanning) and foreign object debris detection, even at the maximum travel speed of 1225 km/h.
In addition to visual inspection, the system provides the value for the width of the gap between every I-beam pair at a resolution of fewer than 0.05 inches and a graph indicating FOD as a function of displacement down the tube.
Preliminary system design - Pictures: RIT team
The need for speed
Dedicated software developed by RIT uses the data obtained to create a 3D model of the tubes, enabling defects in the material to be detected during operation.
This means that changes can be identified immediately and any repairs can be planned efficiently.
The use of existing image capturing technology and standard products available at any time make the development, integration, and operation of this inspection system particularly efficient and cost-effective.
Despite the efficiency, the requirements for the camera system to be used were extremely demanding.
The use of structured light calls for a very good image quality and exceptional camera and projector resolution.
In particular, the cameras must have an excellent signal-noise ratio and a high dynamic range.
High speeds require high frame rates of 500 frames per second, and a corresponding camera interface with high bandwidth.
A compact construction, low purchase costs, and easy usability were further requirements for use in the Hyperloop project.
Rail sca from the top - Pictures: RIT team
Choose wisely
"To select this critical system component, we compared over a dozen different cameras. We chose XIMEA because of the reliable high frame rates and the compact form factor. We were also very impressed by the easy integration, competitive purchase cost, and the personal, friendly service", said Carrucci.
For the Hyperloop MARS (Mechanized Autonomous Rail Scanner) maintenance system, the RIT team is using two MQ003 cameras from xiQ line.
Based on ams CMOSIS CMV300 sensor with 7.4 µm pixel size and 60 dB Dynamic Range, these cameras deliver more than 500 fps in VGA resolution, at 8 bits per pixel.
The CMOS Global Shutter technology guarantees a high image quality with no smearing even at high speeds, ensuring precise 3D analysis.
The sensor is combined with 5 Gb/s super-speed USB 3.0 interface that ensures rapid transmission of the images with no frame loss and easy integration.
The data is transmitted uncompressed in real time directly to a computer running fast GPU and FPGA hardware.
All this is embedded in an extremely compact camera housing with C-Mount (or CS) that measures just 26 mm x 26 mm x 24 mm and weighs only 26 g.
Even though XIMEA xiQ cameras consume very little power – mere 1.5 Watts – and generate minimum heat, another Hyperloop partner, responsible for the design of the transport capsules, developed a special camera box/enclosure for it, to compensate for the lack of air-cooling when used in the vacuum of the Hyperloop tubes.
ITIC suitable for vacuum with XIMEA MQ003 – Picture: RIT Imaging Team
Ladies and Gentlemen, start your engines
In addition to MARS, the RIT team has developed two more imaging-based maintenance systems for SpaceX, which are required as part of the Hyperloop project to monitor the tunnel walls and can also be used in the space program.
In first, the developers are also putting their faith in XIMEA cameras for a system known as VALMAR - Very Accurate Length Measurement And Review.
A robot runs autonomously over the steel girders using laser scanning with an accuracy of under 1 mm to detect possible irregularities or foreign bodies on the rails.
With the second additional system, ITIC (Intra-Tube Inspection of Condition) SpaceX is able to surveil the interior of the tube with high-speed imagery.
The first test runs of the Hyperloop project begun in January 2017 in Quay Valley, California. Stay tuned.
Robot system for rail monitoring – Picture: RIT
Related articles
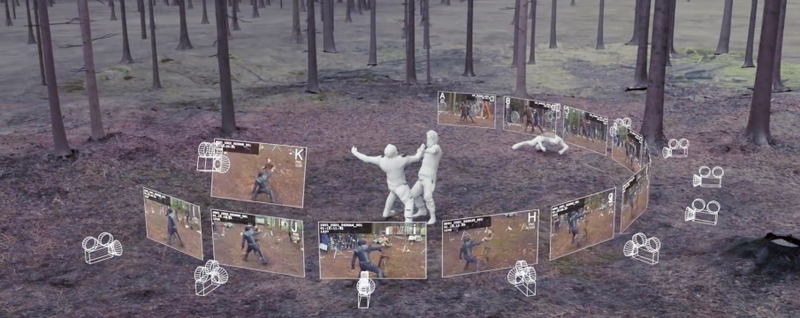
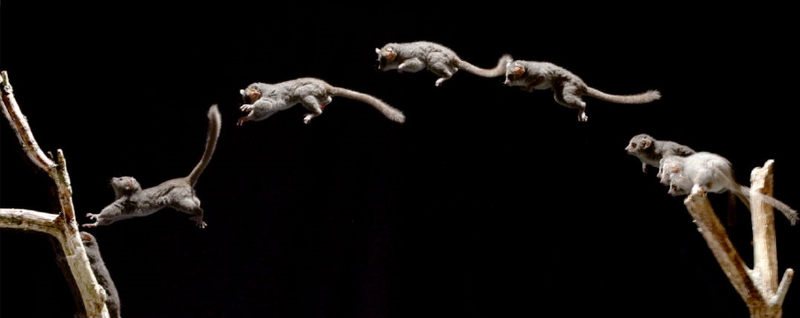
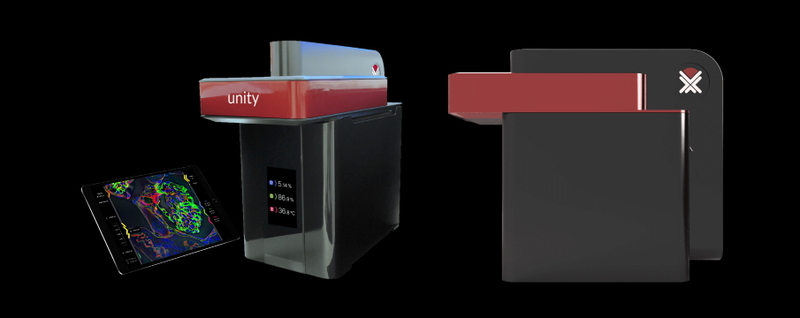
Latest articles
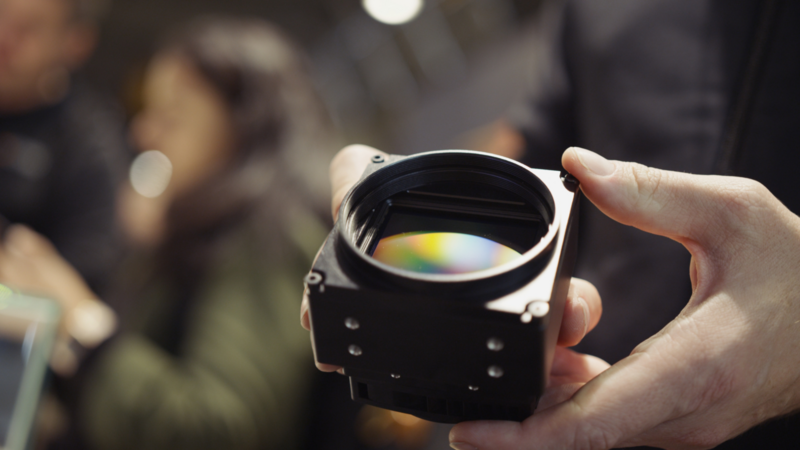
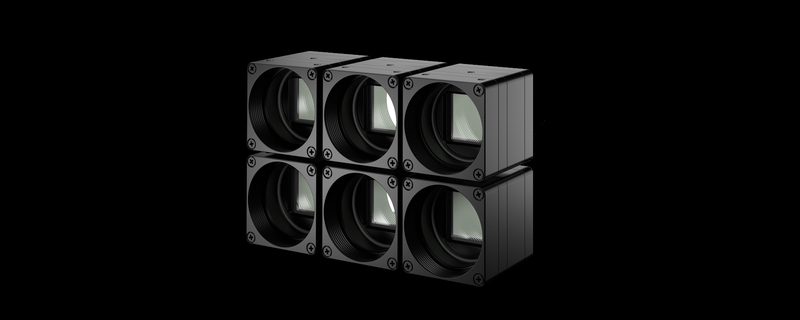
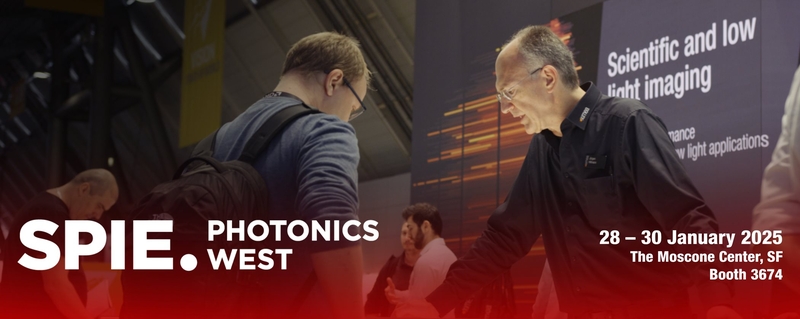
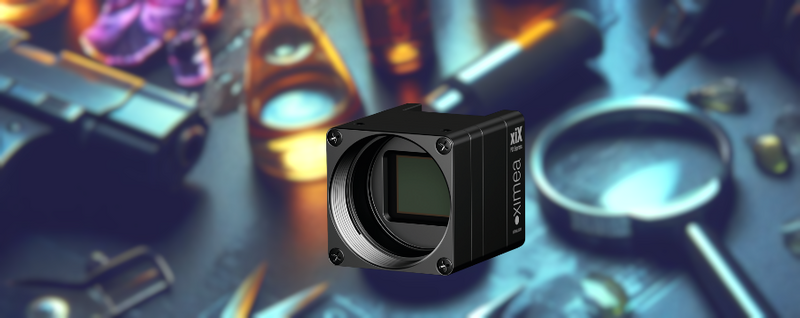
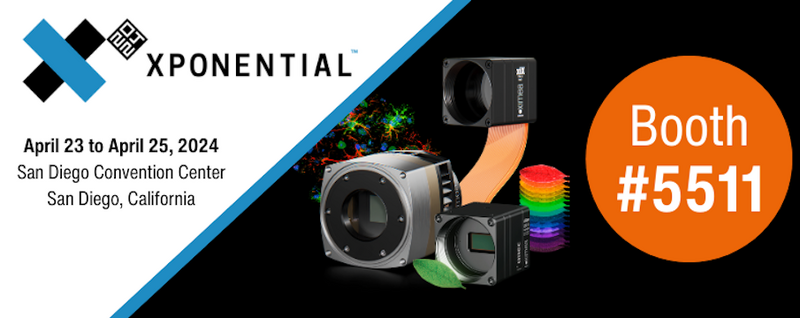
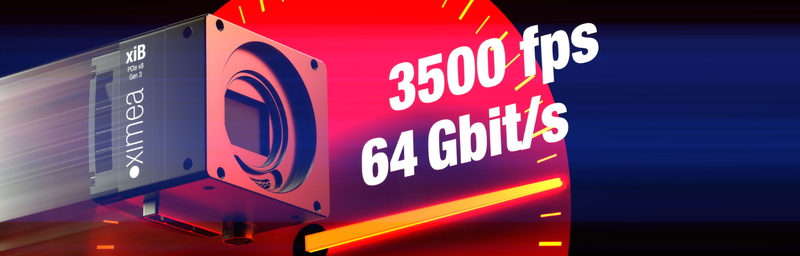